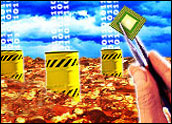
Part 1 of this series explores the markets and industries surrounding polymers in computing. Part 2 investigates electroactive polymers. Part 3 details the development of organic polymer memory devices.
Nurdles. Aglets. Bakelite. Cellophane.
There’s poetry in the myriad names of plastic, which seems fitting for a man-made substance that barely existed prior to World War II but will most likely outlast human civilization itself.
And that’s just the 100 billion tons of the stuff we’ve created so far.
Simultaneously a boon and a scourge, synthetic polymers — endlessly malleable, far-flung and nearly indestructible — are a technical marvel requiring a technological cure.
The elaborate chemical processes which form the rich variety of commercial plastics that we use so extensively also pollute both our air and water, while discarded plastic end-product waste contaminates our landfills and oceans.
As an extreme example, the North Pacific Subtropical Gyre is a ringlike system of rotating ocean currents between California and Hawaii. Known colloquially as the Great Pacific Garbage Patch, this mid-ocean area, which is the size of a small continent, is covered with millions of tons of floating plastic. The detritus bobbing around on the surface includes cups, bottle caps, tangles of fish netting and monofilament line, bits of polystyrene packaging, six-pack rings, spent balloons, filmy scraps of sandwich wrap, and limitless limp plastic bags. And that’s just the visible part. Also, the planet has six other major tropical oceanic gyres, each of them swirling with their own pools of ugly plastic flotsam, debris and refuse.
The near-catastrophic results from creating a product that cannot be properly disposed of has finally pushed the polymers/plastics industry into “high-alert” sustainability mode.
Going forward, industry companies face accountability and responsibility demands from the public and the government (e.g., restriction of hazardous substances, or RoHS, directive requirements), and they are looking to technology for help in solving their problems.
But achieving sustainability is a huge undertaking because it involves the entire inter-connected chain of product design, source materials supply, manufacturing, distribution, consumption, waste disposal and recycling. Some notable developments in synthetic polymer sustainability advances include:
- “Polyware” applications — e.g., digital prototyping, simulation, computational modeling and structural analysis, in addition to entire enterprise resource planning (ERP) business management systems — are changing the ways synthetic polymers are designed, produced and marketed.
- “Green” polymers made of natural substances (even garbage) are replacing petro-polymers.
- “Cold and clean” manufacturing processes seek to eliminate volatile organic compounds (VOCs) and minimize greenhouse gas (GHG) emissions.
“The biggest technical challenge will be to provide the level of performance required, meet environmental compliance issues, and do all this with the right cost/performance balance,” said Jeffrey T. Gotro, president of InnoCentrix, a California-based consulting firm serving the polymer industry.
“The synthetic polymers used in the future need to be environmentally friendly,” Gotro told TechNewsWorld. “Emerging new biopolymers will need to meet high-temperature stability requirements, have low moisture absorption and be environmentally sustainable in order to find use in electronics.”
PolyWare
Computational modeling of polymer processing and synthesis plays a key part in the development of better processes and products. Predictive models for reaction pathways can enable polymer scientists to improve reaction selectivity and create fewer undesirable byproducts and wastes.
Finite element analysis (FEA), used in new product design and existing product refinement, involves computer modeling of a material that is stressed and analyzed for specific results to determine a proposed part’s structure and essential features. FEA is useful in modeling configurations like polymers that have complicated geometries and incorporate various materials. Elements can be as small or as large as needed to facilitate the analysis, and the electrical properties of each element can be defined independently.
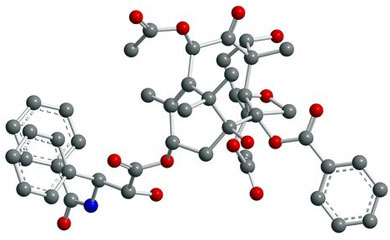
In many finite element simulations of synthetic polymer components, the most challenging step is the specification of an appropriate material model that captures the experimentally observed non-linear “viscoplastic” response of the material.
One company meeting such challenges is Veryst Engineering, which provides services for the design, manufacturing and failure analysis of polymeric parts and components. Much of the company’s work is based on advanced characterization and physically based computer models to solve industrial problems involving polymer systems.
The company has developed a library of user-material models that capture the response of elastomers (rubber), biomaterials, thermoplastics and thermosets. These material models can be added to commercial FEA software as an external library in order to boost accuracy in simulations and predictions of real polymer materials.
C. Brewer Company, a precision plastic injection molding firm, uses two other versatile applications in its plastic production operations: Autodesk Moldflow injection molding simulation software, and IQMS‘s EnterpriseIQ-realtime ERP software specially designed for the injection molding plastics industry.
Moldflow, part of the Autodesk solution for digital prototyping, provides tools that help manufacturers study the injection molding process and optimize the design of plastic parts and injection molds. Companies worldwide use Moldflow simulation software to help reduce the need for costly physical prototypes and get products to market faster, while also avoiding potential manufacturing defects that add to waste.
EnterpriseIQ, popular ERP software among plastics manufacturers, integrates all aspects of a business (accounting, production, inventory, HR, etc.) into one centralized information system. Organizations looking for ways to make environmental manufacturing sustainability strategies work can turn to the supply chain operation to manage the costs of energy, emissions and waste in sourcing, manufacturing and logistics. Use of ERP software can better position companies to integrate data coming from manufacturing, HR and supply chain systems for improved control of both production processes and products alike.
Superior knowledge across the board leads to better control of sustainable outcomes, according to C. Brewer CEO Chuck Brewer III.
“With proper identification, all the materials we make can be recycled and reprocessed with a small compromise to their original physical properties,” Brewer told TechNewsWorld. “The challenge then is in educating the end user, who often associates plastic as being cheap and disposable.”
PolyGreen Productions
The reduction of waste and toxic emissions in polymer processing and synthesis is a critical factor in achieving sustainability within the industry. Synthetic polymer manufacturing has traditionally involved the use of volatile organic compounds (VOCs), solvents and water and has required extensive separation and containment processes to ensure that harmful materials do not enter the environment. Reduction of pollution and waste can be achieved through better management of chemical reactions and improvements in recycling and recyclability. The specific performance targets that relate to this goal include: reduction of water use in polymer processing, increasing the markets for byproducts, and increasing the biodegradability of synthetic polymers like plastic.
Pre-formed plastic consumer product packaging (e.g., blister packs and clamshells) is a multi-billion dollar business with a central problem that neatly captures the complexity of achieving sustainability in the manufacture and use of synthetic polymers.
Because thermoplastics like PVC (polyvinyl chloride) are glassy and non-porous and so don’t readily absorb ink, printed graphics and other product-related manufacturer and consumer information have to be provided on internal pre-printed paperboard cards or external paper labels and stickers. These paper-based materials can add as much 25 to 30 percent to the cost of a product while producing an abundance of paper waste.
Proactive Packaging & Display is dedicated to providing 100 percent sustainable consumer products packaging. The company deals with the thermoplastic printing issue by using a sustainable technique involving web offset printing technology and electron beam (EB) curing.
A continuous roll of thermoplastic material is fed through a printing press, which transfers text and images made from a reactive and usually solvent-free ink to one side (or both, if required) of the print medium. Radiation curing utilizes electron beams to polymerize the coating material. Following printing and curing, the treated thermoplastic is cut into sheets, which are separated and sized for thermoforming into discrete packages.
“Organic inks and coatings and EB curing don’t require light or heat and use far less power while emitting far fewer greenhouse gases than possible with conventional offset processes,” said Gary Hartog, CEO of Proactive.
“There are no emissions, VOCs or other air pollutants produced in this clean process,” Hartog told TechNewsWorld.
Castor Oil vs. Petro
Fossil fuels like petroleum — inexpensive, abundant and water resistant — have long dominated the plastics market. Oil and plastic mix too well, though, and the marriage hasn’t been so good for the planet in terms of resource depletion, pollution, global warming, habitat destruction and other assorted environmental ills. Petroleum-based polymers derive from an exhaustible resource, require the use of toxic and hazardous chemicals in their production and are central to the problem of solid waste disposal.
To deal with environmental impacts from synthetic polymers in the post-production, post-consumption waste and recycling chain, the plastics industry is responding with solutions like biodegradable plastics made from organic feedstocks instead of petrochemicals.
Agriculture-based polymers promise an environmentally friendlier alternative to petroleum-based polymers.
Most of these “bioplastics” are made from plants like corn, soy, sugar cane and switch grass, but scientists have recently turned to trash in an effort to make so-called “green polymers,” essentially plastics processed from garbage-orange peels, potato peels, olive oil, chicken feathers, etc.
Nature’s abundance doesn’t end there. China-based Evonik Industries has developed new polyamides produced fully or partially from monomers obtained from the bean of the castor oil plant.
Other poly-options include e. coli bacteria and carbon dioxide.
But recent studies have demonstrated that, while biopolymers can indeed be made from renewable sources, detailed life cycle assessment (LCA) studies indicate they are often not as environmentally favorable as some traditional fossil fuel-based polymers, according to InnoCentrix’s Gotro.
“This is an interesting and unexpected result,” he said.
An Oct. 2010 study from the University of Pittsburgh’s Swanson School of Engineering and the National Science Foundation supports this view.
Pitt researchers examined 12 plastics — seven petroleum-based polymers, four biopolymers, and one hybrid. The team first performed an LCA on each polymer’s preproduction stage to gauge the environmental and health effects of the energy, raw materials and chemicals used to create one ounce of plastic pellets. They then checked each plastic in its finished form against principles of green design, including biodegradability, energy efficiency, wastefulness and toxicity.
Biopolymers were among the more prolific polluters on the path to production, according to the LCA. The team attributed this to agricultural fertilizers and pesticides, extensive land use for farming, and the intense chemical processing needed to convert plants into plastic.
The Pitt researchers found that while biopolymers are the more eco-friendly material, traditional plastics can be less environmentally taxing to produce.
Once in use, however, biopolymers bested traditional synthetic polymers for overall eco-friendliness.
There are no easy answers for companies trying to choose between the newer biopolymers and the petro-polymers they’ve used for decades. Even recycling has its challenges.
“Recovering and separating the plastic from high tech devices is costly,” plastics industry consultant Debbie Hauser told TechNewsWorld. “Ultimately, a hybrid of virgin resin plus regrind becomes more expensive than just virgin resin alone. This is the case in the plastic bottle industry. Because the U.S. has not adopted incineration of polymers as a means to generate energy, the plastic becomes land fill.”
So, what can manufacturers of synthetic polymers do about achieving sustainability? For starters, they can set their goals around a definition of sustainability provided by the U.S. Dept. of Commerce’s Sustainable Manufacturing Initiative (SMI):
“The creation of manufactured products that use processes which minimize negative environmental impacts and are non-polluting, conserve energy and natural resources, are economically sound and are safe for employees, communities and consumers.”
No easy task, certainly, but all that’s at stake is the future of our world.
Fantastic Plastic, Part 1: Polymers in Computing